Ronan took his class out to visit several potter's studios in the Penland area while I was there. I was excited to hear that they were going out to
Stanley Mace Anderson's pottery, so I decided to go along too.

Stan is an icon in the majolica world. He's been producing his unique style of majolica pottery since the late 70's. (See article
HERE).
Stan was very generous and talked to us all about his pots and process. I love Stan's brushwork and the expressive quality of his forms and decoration. He had shelves of work waiting to be decorated.

He had been working here at his wheel on some trays when we arrived.
This next image is one of the most amazing things I've ever seen in a workshop. Stan's pots of colored stains. I imagine these have been 'growing' here as they have been used over the past 2+ decades.

There were also shelves full of finished works. Cups, yunomi, bowls of various sizes, many, many plates, platters, and other tableware. All useful, all beautiful and rich in color. I had to have a yunomi.
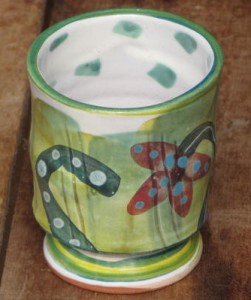
Stan shared that he has been brushing some white slip onto the work at the leather hard stage. This is not normally done in majolica. The slip is loosely brushed over certain areas and sometimes he will scratch through it. The slip gives some sense of movement under the majolica glaze and the marks give some texture. I thought this was really brilliant.
I totally fell in love with the separately thrown and added foot on the yunomi.
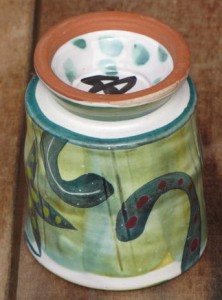
I'll be trying this soon. Stan also does this on some tall footed bowls and tureens, as well as ewers and tall teapot forms.
This is the first majolica pot I have ever bought!! I am happy that it's one of Stan's and I'm pretty sure next time I go back I'll be getting a plate.